Comprehensive Overview: What is Porosity in Welding and How to Prevent It
Comprehensive Overview: What is Porosity in Welding and How to Prevent It
Blog Article
The Scientific Research Behind Porosity: A Comprehensive Overview for Welders and Fabricators
Understanding the intricate mechanisms behind porosity in welding is important for welders and makers striving for remarkable craftsmanship. As metalworkers delve into the midsts of this sensation, they reveal a globe controlled by numerous aspects that influence the formation of these tiny voids within welds. From the make-up of the base products to the intricacies of the welding process itself, a plethora of variables conspire to either aggravate or ease the visibility of porosity. In this detailed guide, we will untangle the scientific research behind porosity, discovering its results on weld high quality and unveiling progressed methods for its control. Join us on this journey with the microcosm of welding imperfections, where accuracy satisfies understanding in the pursuit of flawless welds.
Understanding Porosity in Welding
FIRST SENTENCE:
Exam of porosity in welding exposes essential understandings right into the integrity and high quality of the weld joint. Porosity, identified by the existence of tooth cavities or voids within the weld steel, is a typical issue in welding processes. These gaps, if not appropriately resolved, can compromise the structural honesty and mechanical residential properties of the weld, resulting in possible failings in the finished product.
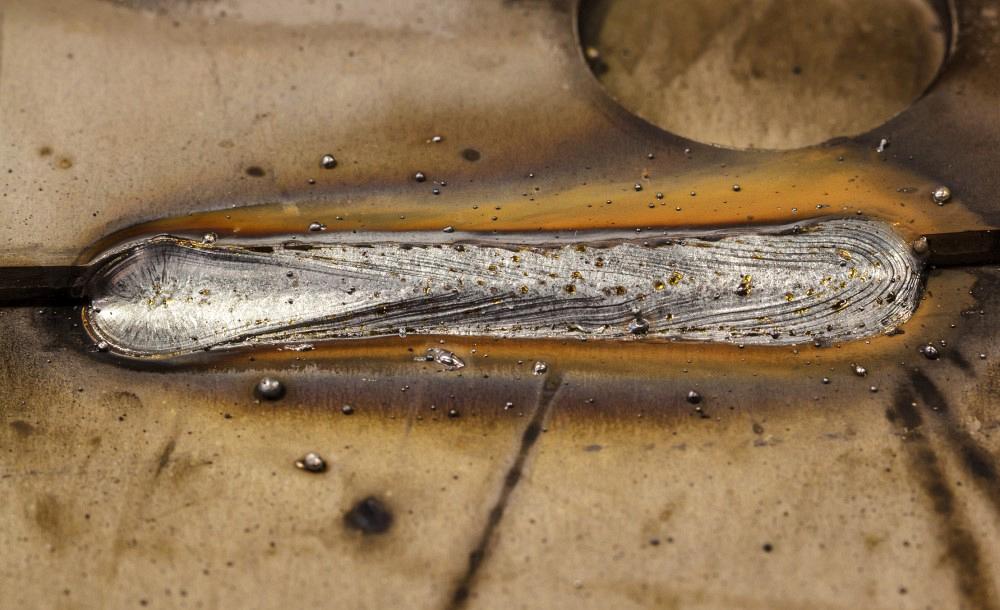
To discover and evaluate porosity, non-destructive screening approaches such as ultrasonic screening or X-ray examination are often utilized. These techniques enable the identification of inner problems without jeopardizing the stability of the weld. By assessing the size, shape, and distribution of porosity within a weld, welders can make informed choices to improve their welding procedures and achieve sounder weld joints.

Aspects Influencing Porosity Development
The incident of porosity in welding is influenced by a myriad of factors, varying from gas shielding effectiveness to the ins and outs of welding criterion settings. Welding criteria, consisting of voltage, current, travel speed, and electrode kind, additionally influence porosity development. The welding strategy used, such as gas metal arc welding (GMAW) or shielded steel arc welding (SMAW), can influence porosity formation due to variations in warm distribution and gas coverage - What is Porosity.
Results of Porosity on Weld Quality
Porosity formation significantly endangers the architectural stability and mechanical residential or commercial properties of bonded visit our website joints. When porosity is present in a weld, it produces voids or dental caries within the material, reducing the total strength of the joint. These spaces work as tension focus factors, making the weld a lot more prone to fracturing and failure under tons. The visibility of porosity likewise weakens the weld's resistance to rust, as the trapped air or gases within deep spaces can respond with the surrounding atmosphere, causing degradation gradually. Additionally, porosity can prevent the weld's ability to hold up against pressure or impact, further jeopardizing the overall high quality and integrity of the welded structure. In vital applications such as aerospace, vehicle, or architectural building and constructions, where safety and durability are paramount, the harmful impacts of porosity on weld quality this article can have extreme repercussions, emphasizing the importance of minimizing porosity through appropriate welding strategies and procedures.
Methods to Minimize Porosity
In addition, making use of the appropriate welding criteria, such as the proper voltage, current, and travel rate, is critical in stopping porosity. Maintaining a consistent arc size and angle during welding also helps lower the probability of porosity.

Making use of the proper welding technique, such as back-stepping or employing a weaving activity, can additionally assist disperse warmth evenly and reduce the opportunities of porosity formation. By implementing these methods, welders can successfully reduce porosity and produce high-grade bonded joints.

Advanced Solutions for Porosity Control
Applying innovative modern technologies and ingenious approaches plays a crucial duty in attaining remarkable control over porosity in welding procedures. One advanced solution is using innovative gas mixtures. Protecting gases like helium or a mixture of argon and hydrogen can help in reducing porosity by providing much better arc stability and improved gas coverage. In addition, using advanced welding techniques such as pulsed MIG welding or customized atmosphere welding can Discover More Here also help reduce porosity issues.
One more advanced option involves making use of advanced welding tools. Making use of tools with integrated features like waveform control and innovative power sources can enhance weld high quality and reduce porosity dangers. Moreover, the implementation of automated welding systems with precise control over specifications can significantly lessen porosity defects.
Moreover, integrating advanced tracking and inspection modern technologies such as real-time X-ray imaging or automated ultrasonic screening can help in spotting porosity early in the welding procedure, permitting for immediate corrective actions. In general, integrating these innovative services can substantially enhance porosity control and boost the general quality of bonded elements.
Conclusion
To conclude, comprehending the scientific research behind porosity in welding is vital for welders and makers to produce premium welds. By identifying the aspects influencing porosity development and applying strategies to decrease it, welders can improve the overall weld high quality. Advanced services for porosity control can even more enhance the welding process and guarantee a strong and trustworthy weld. It is necessary for welders to continuously enlighten themselves on porosity and implement finest practices to achieve optimum results.
Report this page